The Big Feast
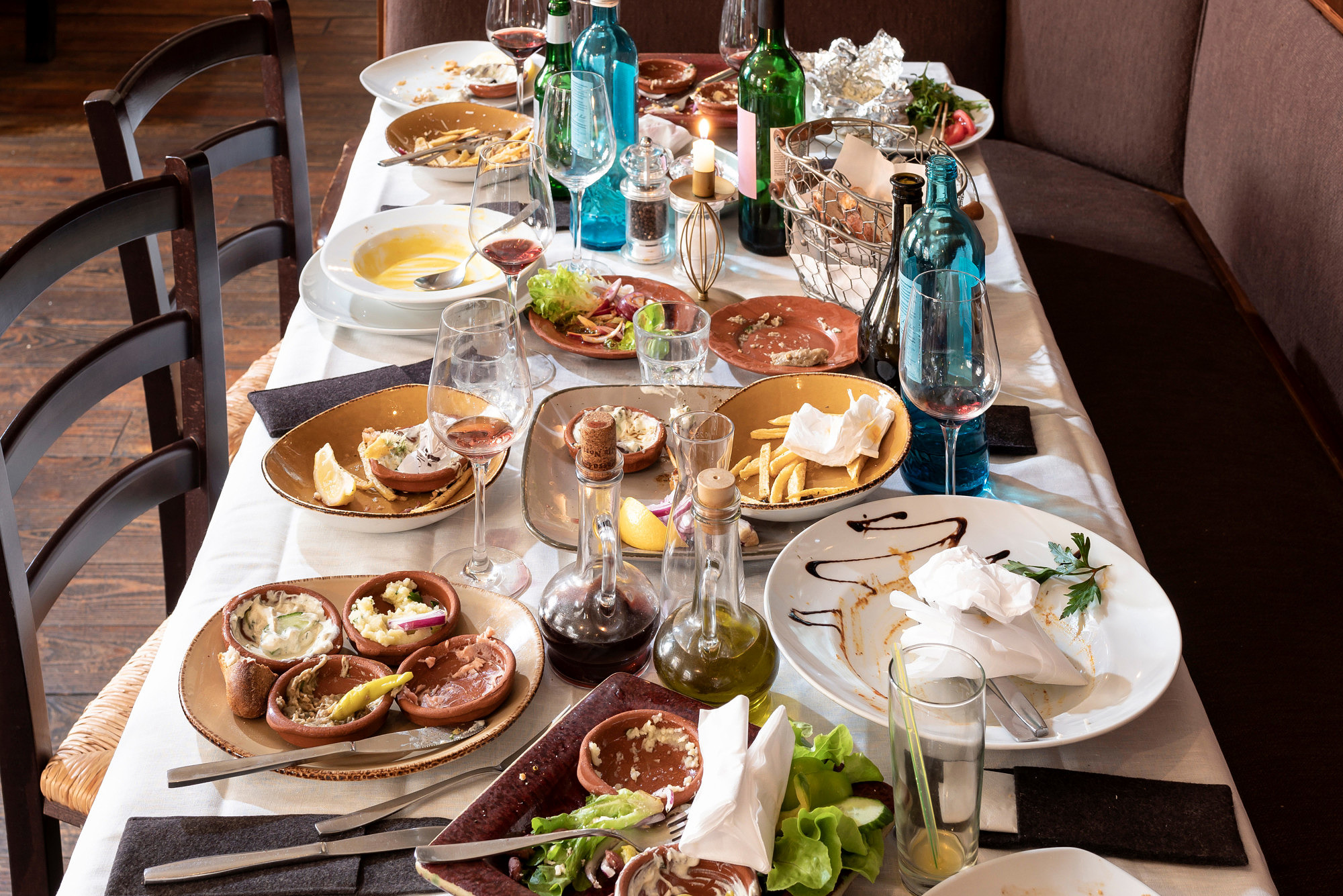
Humans have been over-exploiting the planet. The result – fossil resources are running out. Scientists at FAU are researching into alternatives
By Luisa Macharowsky and Andreas Kunkel
‘It’s 2125 and the last supplies of coal are being shared out. They will probably only last around a month, at most. Gas and crude oil ran out about fifty years ago. There hasn’t been any zinc, gold, tin, silver or nickel since 2033. More and more resources that our technology and society depend on are slowly running out…’
This is what the near future could have in store for the human race. Humans are dependent on natural raw materials. Several developments in history would not have been possible without them. Coal, for example, literally fuelled advances in technology. Other resources such as natural gas and crude oil have been used to generate energy all over the world for a long time now. However, other substances such as gold and silver, which we may initially associate with sparkling rings and necklaces, are very often used in industry and we encounter them (without necessarily knowing it) in our daily lives. Mobile phones, computers, pacemakers, or the electricity supply simply would not work without these precious metals.
Reckless
Despite all their technological advances in the use of raw materials, humans seem to have forgotten one thing – there is only a limited supply of all these materials. To maintain and improve standards of living, humans are increasingly over-exploiting the planet by taking more and more and digging deeper and deeper. According to the The Use of Natural Resources Report for Germany 2016 issued by the German Environment Agency, the population of Germany used 1.3 billion tonnes of raw materials in 2011 alone, that’s 16 tonnes per head or almost 44 kilos per day. This is equivalent to each person in Germany using 1.8 kilos of raw materials every day. 21 percent of this is from fossil fuels, which is equivalent to 273 million tonnes each year. And that’s just one country.
A threshold was crossed in 1971, the year humankind started using more resources per year than can be replenished naturally, and supplies are dwindling at an increasing pace. At the moment, we need one and a half times the resources that the Earth can provide. A rethink is already taking place, however, and scientists all over the world are researching into replacements for fossil fuels. Scientists at Friedrich-Alexander-Universität are also looking into ways of replacing natural resources with sustainable materials in various projects.
Printable solar cells
The idea of using solar energy as a renewable energy source is not new. Electricity from conventional solar cells has been a competitive alternative for a long time. But it’s not without disadvantages. High temperatures are required for manufacturing silicon solar cells, using a large amount of energy in the process. The amount required is so great that it takes two to four years for the energy balance to reach zero.
This is not the case with the solar cells being developed by researchers under the leadership of Prof. Dr. Christoph Brabec at the Chair of Materials Science. They need a temperature of only one hundred degrees during the manufacturing process and are simply printed onto the surface of various materials – the technology used is similar to that of an inkjet printer. These cells pay for themselves in a few weeks.
They are also thin, flexible, transparent, and colourful. They can be incorporated in the façades or windows of buildings and used as design elements. ‘We want to produce energy where it’s needed – in cities and not in fields’, says Brabec.
The scientists at FAU use organic and perovskite (inorganic) semiconductors and quantum dots, a nanostructure that also consists of semiconductors, during the manufacturing process. The groups of materials used are relatively new and have thus not yet been well researched, but they are highly efficient. The research carried out by FAU materials scientists pays off. The printed solar cells have an efficiency of 21 percent with room for further improvement. As a comparison, conventional solar cells that have been researched for 40 years longer than these printed cells have an energy efficiency of almost 27 percent.
‘During our research, we not only focus on the efficiency, but have the product as a whole in mind. The solar cell should be stable, durable and cost efficient, and above all, environmentally friendly. We are trying to develop a manufacturing process that doesn’t need heavy metals and materials that contain chlorine. Our vision is for the cells to be printed at home and in large printing companies that meet European environmental requirements’, emphasises Brabec.
Platinum is silver, calcium is (sometimes) gold…
Platinum has been the ideal catalyst for numerous chemical reactions for over 200 years as it can split the molecules from hydrogen, oxygen and other gases into single atoms. The element is therefore used not only as an oxidisation catalyst in vehicles but also in nitric acid manufacturing or in the pharmaceutical industry. However, the element’s use in the health sector is rather problematic. Platinum, in its complex form at least, is highly toxic and can accumulate in DNA. And platinum is considerably more expensive than gold. Despite these facts, the benefits of platinum have been seen to outweigh its disadvantages.
This could be about to change fundamentally due to the work being carried out by Prof. Dr. Sjoerd Harder, Chair of Inorganic and Organometallic Chemistry at FAU. In his research, he has shown that catalysis is also possible with the comparably uncomplicated element calcium instead of platinum. This means that calcium can be used, for example, for the hydration of imines, which are a special group of chemical compounds. Until now, platinum or other precious metals have always been required for this process. Although replacing these precious metals requires larger amounts of calcium, the technical outlay is comparably low and costs also remain low, according to Prof. Harder. His findings are significant for the pharmaceutical industry in particular, where replacing toxic platinum catalysts with harmless calcium catalysts would provide several advantages.
‘We won’t be able to replace platinum completely as it is a so-called transition metal that can easily activate several molecules’, says Harder. However, there are already a wide range of examples in organic synthesis that demonstrate that calcium is an excellent substitute for platinum. This represents a true paradigm shift.
Prof. Harder does not hold out much hope, however, that these results could soon be used in industry. ‘We are still very much in the early stages as far as this application is concerned, although fundamental research is making rapid progress in replacing platinum in individual applications’.
Fuel of the future
Replacing fossil fuels has been the aim of energy policy in Germany for several years. Hydrogen could provide the solution. Its energy density per weight is three times higher than that of petrol and even two hundred times higher than that of batteries in electric vehicles. When used in a fuel cell, hydrogen is converted into water by an electrochemical reaction with oxygen. This process generates electricity without producing contaminants.
The challenge up to now has been the low energy density of hydrogen per volume. The existing technology that involves condensing hydrogen at high pressure down to minimum volumes is expensive and complex. Storing hydrogen in liquid form is also far from easy as it requires temperatures of -253 degrees Celsius. A team of scientists at FAU led by Prof. Dr. Wolfgang Arlt, Prof. Dr. Eberhard Schlücker and Prof. Dr. Peter Wasserscheid have therefore developed a method that could be the ideal solution: using LOHC (liquid organic hydrogen carrier) technology to chemically bind the hydrogen gas in a special oil mixture. This method makes storing and transporting hydrogen considerably cheaper and safer than using the high pressure gas tanks used so far. Even existing infrastructure such as fuel trucks and tank storage facilities could continue to be used. Hydrogenious, a young company and FAU spin-off, has now successfully brought the process to market maturity.
There is still a lot of research to be done on the subject, as the molecular processes that occur during storage are not yet fully understood. Chemists at FAU are therefore conducting fundamental research on the approach taken by the chemical engineers. Prof. Dr. Jörg Libuda and Prof. Dr. Hans-Peter Steinrück from the Department of Chemistry and Pharmacy are investigating various hydrogen carriers and are incorporating hydrogen into these molecules under strictly controlled conditions. They are interested in discovering in detail how the relevant processes occur on the surface of solid catalysts. ‘We’re dealing with relatively complicated molecules in liquid hydrogen carriers. The aim is to incorporate the hydrogen in the designated position as quickly as possible so that we can create high performance storage units’, says Libuda. The scientists have to deal with a large number of intermediate products that are created when hydrogen is released from the carrier liquid and unwanted by-products can also be generated if the process is not properly conducted. What is the ideal carrier substance for hydrogen? ‘It should react reliably, have a high storage capacity, be easy to obtain and non-toxic. It should also remain in a liquid state in a suitable temperature range, as it must not freeze in winter’, says Libuda. The price is also a factor, of course. The heat transfer oil dibenzyltoluene, which has been used in industry since the 1960s, is currently the best carrier available. The fact that this well-known material can be used as a highly-effective hydrogen carrier is a central innovation of the researchers at FAU and has been decisive in paving the way for the commercialisation of the LOHC technology. The researchers’ success was recently recognised by their nomination for the German Future Prize 2018.