Prof. Dr. Paul Steinmann awarded second ERC Advanced Grant
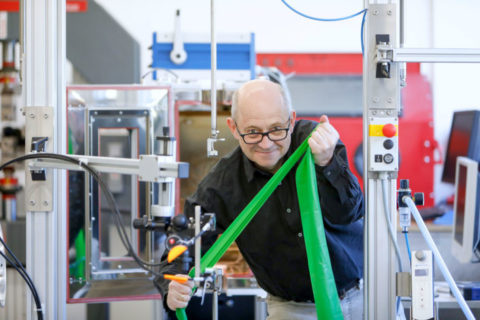
2.5 million euros of funding for five years
The Faculty of Engineering at Friedrich-Alexander-Universität Erlangen-Nürnberg (FAU) has once again been recognized for outstanding achievements: Prof. Dr. Paul Steinmann, Chair of Applied Mechanics, has been awarded an Advanced Grant from the European Research Council (ERC). Professor Steinmann intends to use the funding worth 2.5 million euros to investigate the fracture mechanics of soft materials such as rubber or tissue more intensively during the next five years. Steinmann received his first ERC Advanced Grant for research into magnetic elastomers in 2011.
The more we know about the properties of materials, the more intelligently we can use them. This includes carrying out research into how combinations of materials tolerate each other, how secure joins are and when components break or tear. Paul Steinmann has been investigating topics such as these for over 20 years. He is a leading expert in modeling and simulating the behavior of materials. In various projects, he has investigated how polymers and ceramics deform under electrical current, how the brains and bones of humans behave under mechanical load, the effects of the micro and meso structures of components created using additive manufacturing or which internal stresses extruded steel is subject to.
Little research conducted on fracture mechanics of soft materials
Steinmann intends to use the ERC funding to perform more detailed research into the fracture mechanics of soft materials such as rubber and tissue. “This behavior is well researched in hard materials such as steel, concrete or hard plastic, otherwise we wouldn’t know how to build bridges, buildings or vehicles properly,” says Steinmann. Hard materials can be analyzed using conventional fracture mechanics, whereby the strain is proportional to the force acting on the material; a behavior that is referred to as being linear. The mechanics of soft materials, on the other hand, are not linear, which makes it difficult to calculate the fracture initiation and the spread of cracks.
In his research project, which Steinmann has named “SoftFrac”, he intends to test new modeling approaches and algorithms that allow the spread of cracks in soft materials to be tracked numerically. Steinmann plans to use experiments to generate comprehensive data about fracture behavior, supported by a high-speed camera that supplies several tens of thousands of images per second. A large proportion of the grant will be used to set up several new positions for staff. “This increased team power will enable us to go way beyond previous investigations and work on completely new problems for the first time,” explains Steinmann. “I am convinced that SoftFrac will herald a new era in the comprehensive research of the fracture mechanics of soft materials.”
Robotic hands and predetermined breaking points
The research will predominantly focus on three applications: Firstly, soft robotics, which is rapidly gaining significance in the automation industry. This particularly involves the grippers of robotic arms, which must be soft enough to handle fragile objects such as glasses, but robust enough to ensure a long operating life. The second application is stretchable electronics, such as wearables that are integrated into clothing, since they have to be both elastic and durable. The third application – tissue engineering – is similar, as the tissues grown for this application are also subject to non-linear fracture mechanics.
However, the purpose of SoftFrac is not only to increase the reliability of soft materials. An improved understanding of fracture mechanics could also lead to applications in which materials are purposely destroyed. Steinmann explains: “Just imagine you could precisely determine when rubber breaks. You could then design retaining straps that ensure, for example, that solar sails in space open or modules uncouple at precisely the desired point in time and without the need for complex mechanical systems. Such soft predetermined breaking points could make risky spacewalks for astronauts a thing of the past.”
About Professor Steinmann
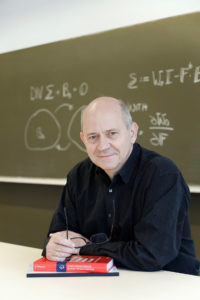
Paul Steinmann has been head of the Chair of Applied Mechanics (LTM) at FAU since 2007. His research areas range from material modeling to multi-scale methods, multi-physics problems, non-standard continua, fracture mechanics, biomechanics and more general aspects of finite elements and discretization methods. Prof. Steinmann is a reviewer for a number of specialist journals, as well as various national and international research organizations. He has been a member of the selection panel for research training groups of the German Research Foundations and of several committees of the German Academic Exchange Service. In August 2021, he was appointed member of the DFG selection panel for the Heinz Maier Leibnitz prize.
In addition to his responsibilities at the Chair of Applied Mechanics at FAU, Steinmann is director of the Glasgow Computational Engineering Centre (GCEC) in the UK. He is also the speaker of the DFG research training group “Fracture across scales: integrating mechanics, materials science, mathematics, chemistry, and physics (FRASCAL)”. He has been the Officer for Strategic Development at FAU since December 2020.
Paul Steinmann has received several awards for his outstanding research, such as Fellow Awards from IACM and EUROMECH (2006), the Timoshenko Visiting Scholar Award from Stanford University (2007), an ERC Advanced Grant (2011) and the Royal Society Wolfson Research Merit Award (2017).